CO₂-reduzierte Zemente - Cemex DE
Innovationen fürs Klima
Innovationen fürs Klima
Mit seiner Future in Action-Strategie strebt CEMEX eine klimafreundliche Produktion weltweit an. Ein wichtiger Punkt dabei: die Entwicklung CO₂-reduzierter Baustoffe und Zusatzmittel. Für diese hat CEMEX das Siegel Vertua® geschaffen. Vertua® kennzeichnet solche Zemente, deren CO₂-Emissionen um mindestens 15 Prozent verringert sind. Die Vertua®-Siegel CLASSIC, PLUS und ULTRA weisen den Umfang der CO₂-Reduktion aus.
„An klinkereffizienten Zementen arbeiten wir bei CEMEX seit mehr als 20 Jahren. Neben Vertua®-Beton haben wir auch Vertua®-Zement eingeführt“, sagt Dr. Patrick Fontana, Head of Product Technology bei CEMEX im Bereich Zement. Er leitet die Entwicklung der klinkereffizienten Vertua®-Zemente am Standort Rüdersdorf. „Mit dem Qualitätssiegel Vertua® möchten wir bei CEMEX Klimafreundlichkeit für unsere Kundinnen und Kunden sichtbar machen.“
CEMEX Deutschland AG
Dr.-Ing. Patrick Fontana
Head of Product Technology Deutschland
patrick.fontana@cemex.com
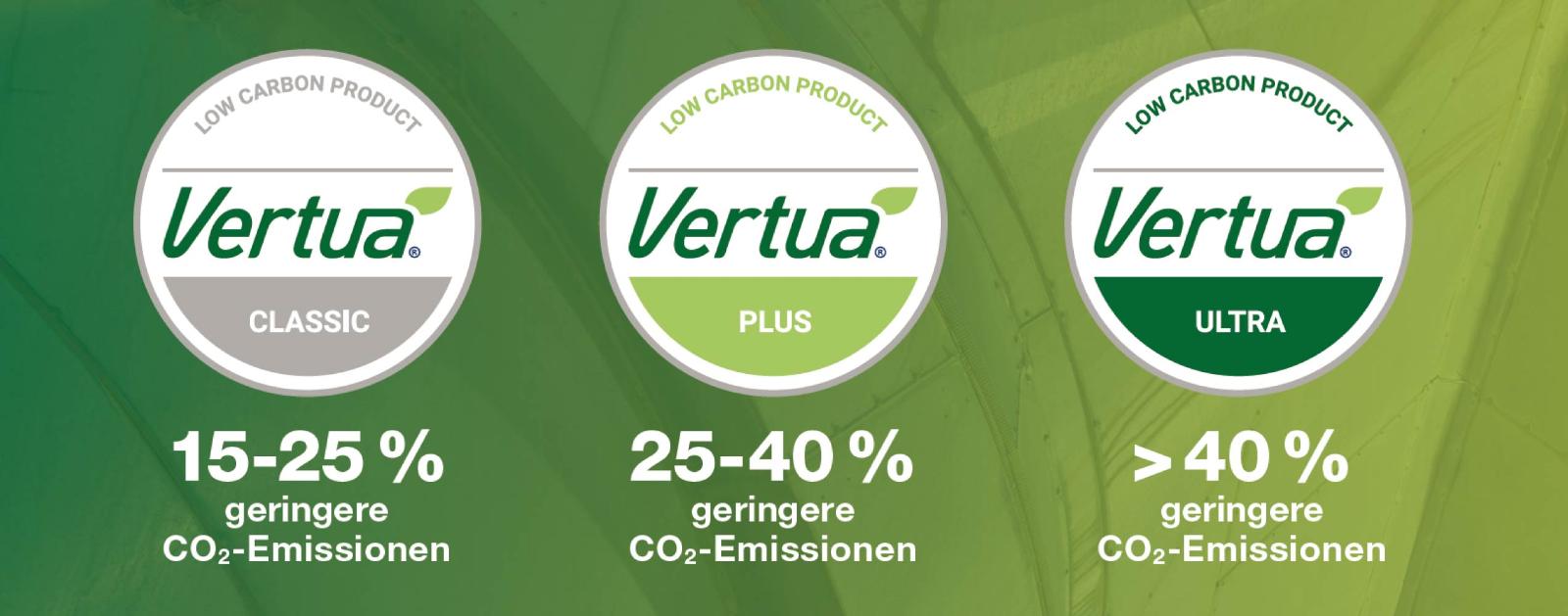
Die Entwicklung eines neuen Zementproduktes kann zehn Jahre oder länger dauern. „Bevor die Zemente großtechnisch hergestellt werden, finden umfangreiche Untersuchungen im Labormaßstab statt“, beschreibt Patrick Fontana den Entwicklungsprozess. „Dabei arbeiten das Baustofflabor und das Qualitätswesen unseres Werkes eng zusammen.“ Neben Klinker werden verschiedene, zum Teil neue Hauptbestandteile der Zemente in unterschiedlichen Feinheiten und Mengen miteinander kombiniert und aufeinander abgestimmt, bis das Produkt bestimmte Zielgrößen erreicht, zum Beispiel bezüglich der Festigkeitsentwicklung und Verarbeitbarkeit. Zusätzlich relevant können auch Sondereigenschaften der Zemente sein, die in speziellen Einsatzbereichen notwendig sind.
Der nächste Schritt ist die Herstellung von Betonen mit den neuen Zementen. „Dabei prüfen wir sowohl Verarbeitungs- als auch Anwendungseigenschaften“, erläutert Patrick Fontana. Um diese Eigenschaften zu optimieren, kooperiert er mit den Kolleginnen und Kollegen von der Bauchemie von CEMEX Admixtures, um das Zusammenwirken des neuen Produkts mit Betonzusatzmitteln wie Fließmitteln und Verflüssigern zu kontrollieren und gegebenenfalls anzupassen.
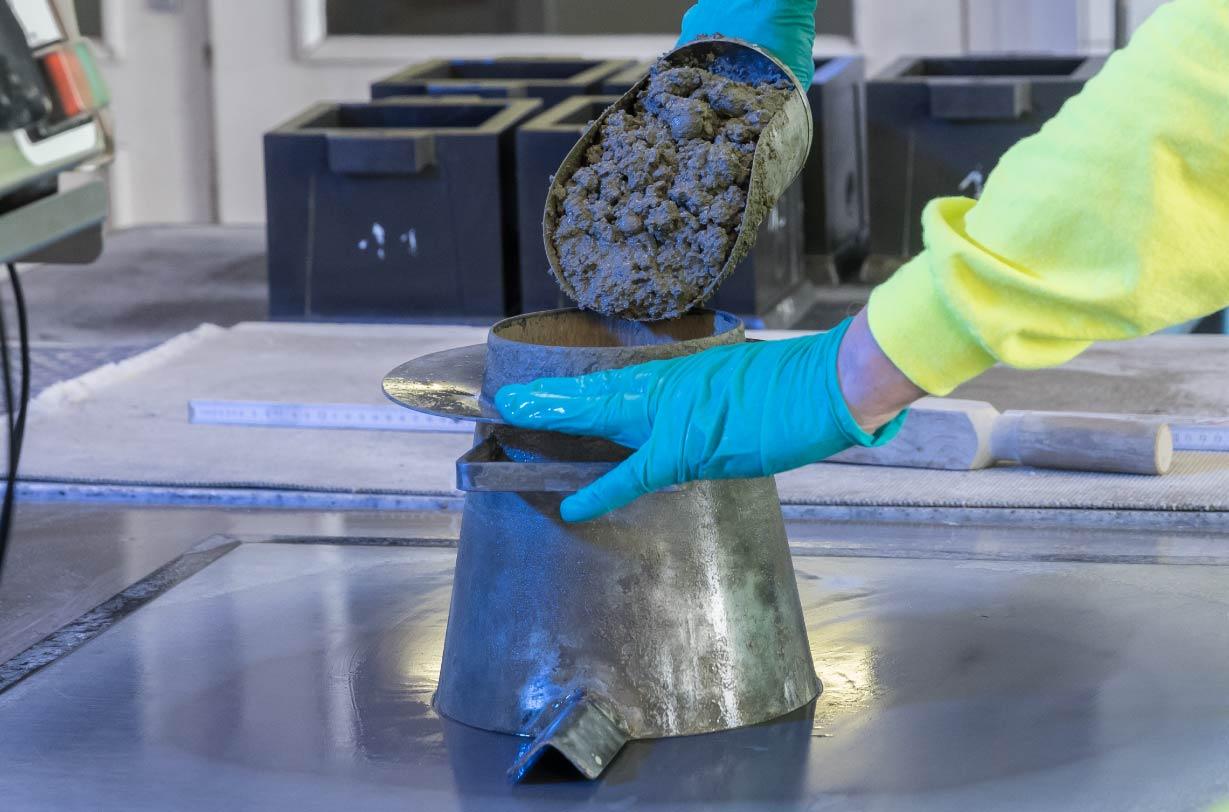
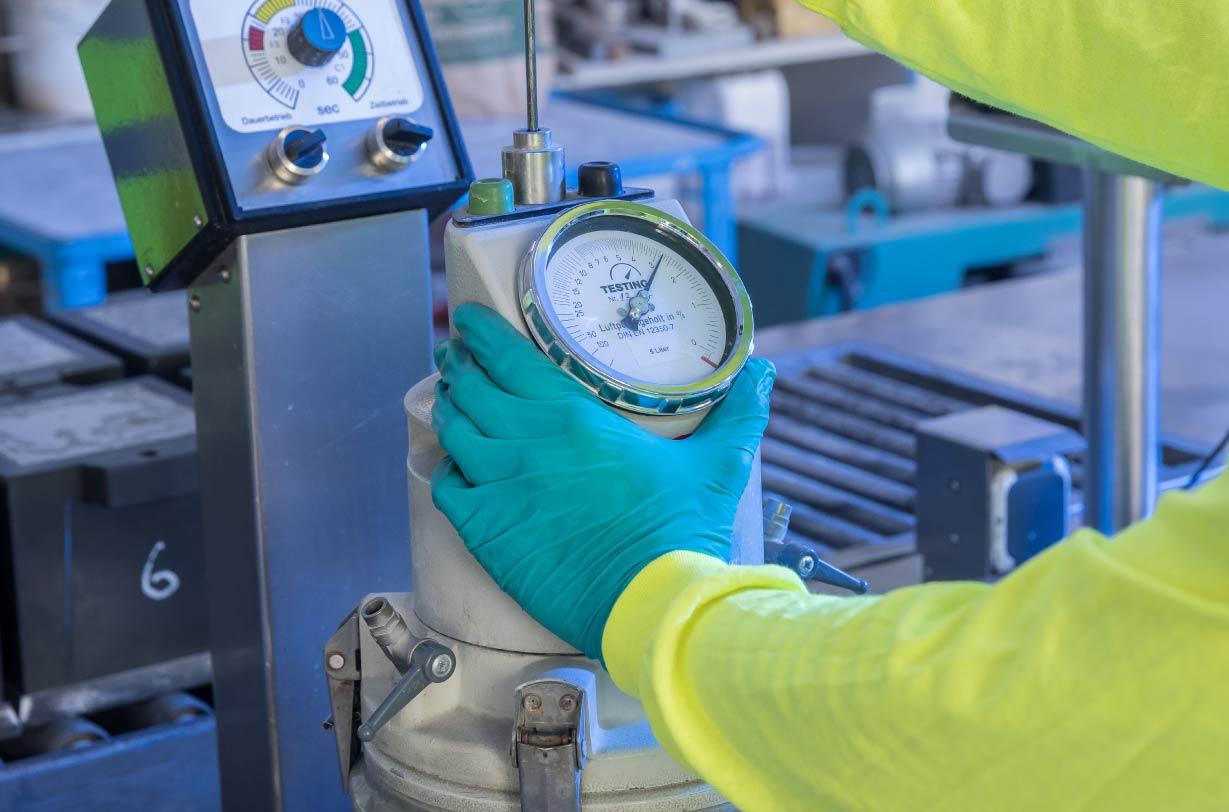
Von der Produktentwicklung zu neuen Normen
Die Entwicklung neuer Zemente geht oft auch mit der Schaffung neuer Normen einher. Denn Voraussetzung für die Anwendung neuer Zemente sind meist bauaufsichtliche Zulassungen. „Unter dem Dach des Vereins Deutscher Zementwerke (VDZ) gab es mehrere Forschungsvorhaben, auch auf internationaler Ebene, aus denen in einem langwierigen Prozess eine weitere europäische Norm für die neuen klinkereffizienten Zemente hervorging“, erklärt Patrick Fontana.
Die Stoffströme der nahen Zukunft sind vage. Daher müssen wir bereits jetzt aktiv alternative Zementhauptbestandteile untersuchen.
Statt CO₂-intensivem Klinker kommen in den Vertua®-Zementen als weitere Hauptbestandteile zum Beispiel Kalkstein und Hüttensand zum Einsatz. Hüttensand ist ein Nebenprodukt der Roheisenerzeugung im Hochofen. „Allerdings gibt es auch bei der Eisen- und Stahlproduktion eine Transformation“, so Fontana. Der Hochofenprozess wird durch klimafreundlichere Technologien ersetzt, sodass etwa ab dem Jahr 2025 weniger Hüttensand zur Verfügung stehen wird. Ob und wie die Zementindustrie Schlacken aus anderen Herstellungsverfahren und Prozessschritten nutzen kann, wird derzeit geprüft. Flugasche ist ein weiterer geeigneter Hauptbestandteil, doch auch sie ist eine endliche Ressource, da der Ausstieg aus der Kohleverstromung bereits beschlossen ist. „Die Stoffströme der nahen Zukunft sind vage. Daher müssen wir bereits jetzt aktiv alternative Zementhauptbestandteile untersuchen“, unterstreicht Dr. Fontana.
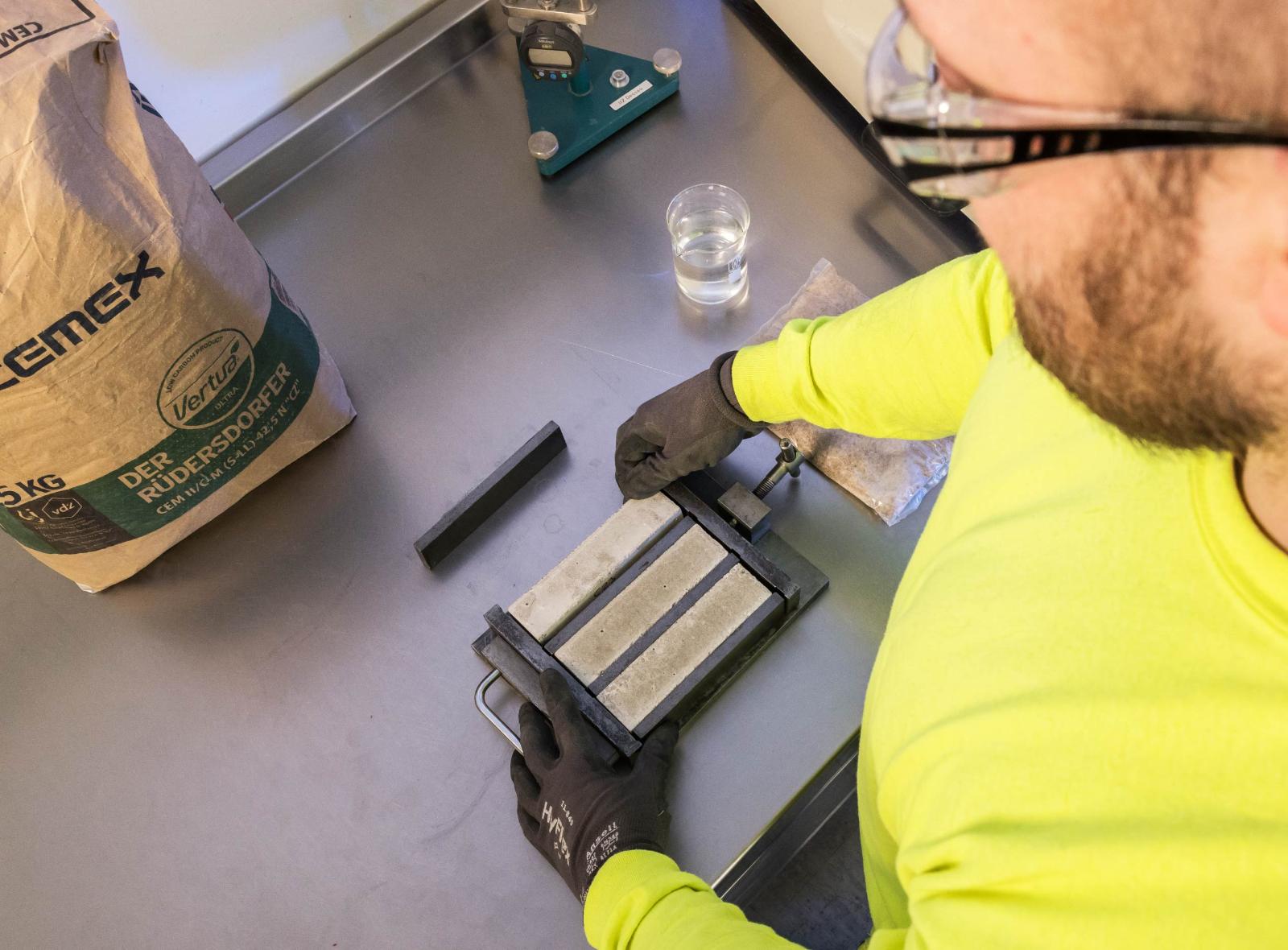
Gleiche Leistung, weniger CO₂
In ihrem Leistungsvermögen sind die Vertua®-Zemente bezüglich ihrer Verarbeitungs- und Festigkeitseigenschaften vergleichbar mit Portlandzementen – und das bei geringerer CO₂-Emission. Die Vertua®-Zemente in der Festigkeitsklasse 42,5 N bringen eine normale Festigkeitsentwicklung mit sich und eignen sich besonders für den Einsatz im Bereich des Transportbetons. Der Vertua® Ultra, ein CEM II/C-M (S-LL), verfügt darüber hinaus aber noch über die besondere Eigenschaft eines niedrigen wirksamen Alkaligehalts. Das heißt, er kann bei alkaliempfindlicher Gesteinskörnung eingesetzt werden, wie sie vor allem in Norddeutschland vorkommt.
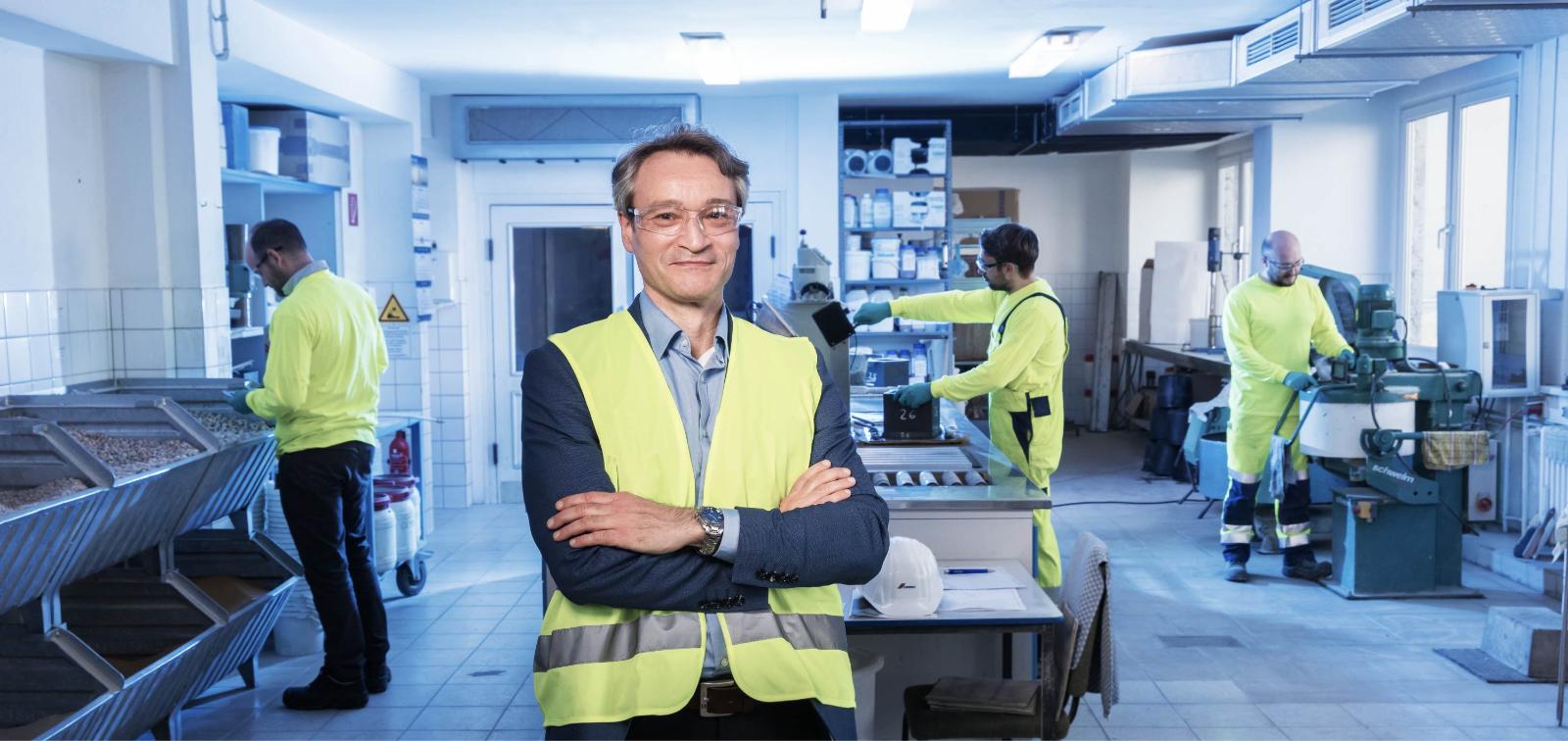
Das könnte Sie auch interessieren:
Unser bauwerk-Newsletter
Abonnieren Sie unseren Newsletter und erfahren Sie mehr über unsere Produkte, Strategie und Innovationen.
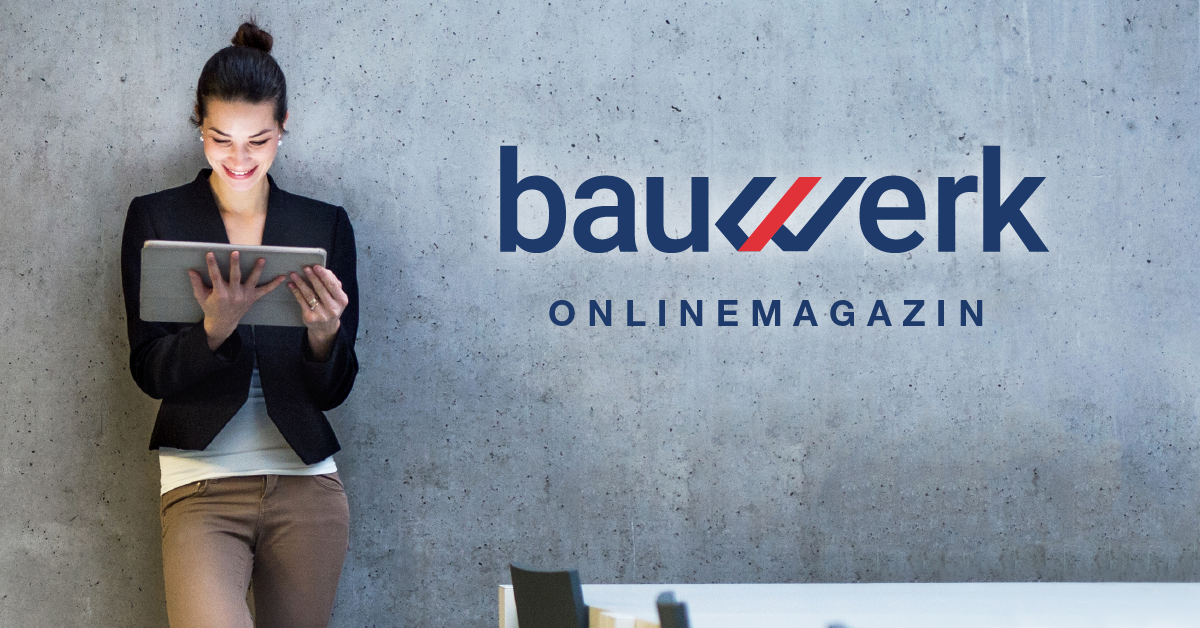