Auf dem Weg zum klimaneutralen Zement - Cemex DE
Auf dem Weg zum klimaneutralen Zement
Auf dem Weg zum klimaneutralen Zement
Stefan Schmorleiz
Werkleiter und Geschäftsführer der CEMEX Zement GmbH
stefan.schmorleiz@cemex.com
Herr Schmorleiz, wie wird der Zement im Werk Rüdersdorf hergestellt?
Stefan Schmorleiz: Das benötigte Haupt-Rohmaterial ist Rüdersdorfer Kalkstein, der im eigenen Tagebau gewonnen wird. Dieser Kalkstein wird zusammen mit kleineren Mengen anderer benötigter Zusatzstoffe wie Sande und Aschen in einem ersten Zerkleinerungsschritt zu Rohmehl gemahlen. Dieses Rohmehl wird im Anschluss in der Ofenanlage auf circa 1450 Grad erhitzt. Hierbei entsteht der sogenannte Klinker, der dem Zement die charakteristischen Eigenschaften liefert, wie z. B. das Erhärten mit Wasser und das Ausbilden hoher Festigkeiten. Der bis zu drei Zentimeter große Klinker wird mit weiteren Zumahlstoffen wie beispielsweise Hüttensand ein zweites Mal gemahlen. Dabei entsteht dann der Zement.
Woher stammen die CO2-Emissionen bei der Zementherstellung?
Stefan Schmorleiz: Heutzutage wird nur etwa ein Viertel unserer CO2-Emissionen durch den Einsatz von Brennstoffen erzeugt. Drei Viertel sind durch den Kalkstein bedingt, der in chemischer Hinsicht zu fast 45 % aus Kohlenstoffdioxid besteht. Dieses wird bereits bei knapp 900 Grad in der Ofenanlage freigesetzt und gelangt in die Atmosphäre. Der Kalkstein ist somit die Hauptquelle unserer CO2-Emissionen im Werk Rüdersdorf.
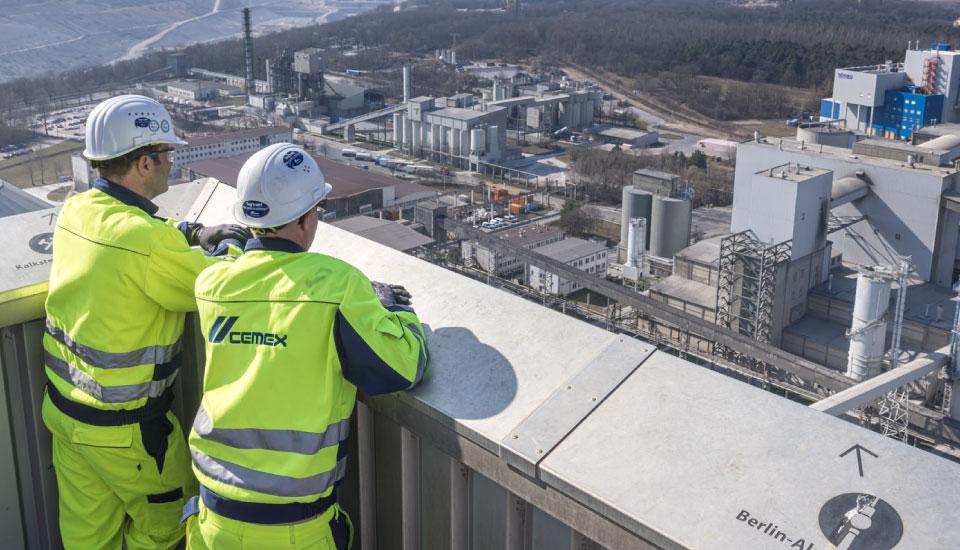
Wie das Zementwerk Rüdersdorf zum Taktgeber der Dekarbonisierung wird
Nachhaltiges Bauen ist eine der zentralen Herausforderungen für den Klimaschutz. Als globaler Baustoffkonzern hat Cemex diese Herausforderung mit seiner Strategie Future in Action angenommen.
Welche Maßnahmen ergreifen Sie, um diese Emissionen zu reduzieren?
Stefan Schmorleiz: Wir arbeiten zeitgleich mit Hochdruck an unterschiedlichen Hebeln. So setzen wir verstärkt biogene Sekundärbrennstoffe ein. Um die für die Zementherstellung notwendigen hohen Temperaturen zu erreichen, heizen wir anstatt mit Kohle inzwischen zu rund 85 % mit Tiermehl, getrocknetem Klärschlamm oder aufbereitetem Restmüll. In Zukunft werden wir diesen Anteil durch gezielte Maßnahmen wie einem eigenen Trockner für Sekundärbrennstoffe auf 95 % steigern. Eine weitere Maßnahme ist die Reduktion des Kalksteinanteils im Klinker. Wir ersetzen den Kalkstein durch Materialien, die dekarbonisiert sind, die also kein weiteres CO2 mehr freisetzen. Dabei handelt es sich um Aschen und Schlacken, die Nebenprodukte aus anderen Industriezweigen sind und dort bereits einen thermischen Prozess durchlaufen haben. Somit ist ihr Einsatz auch ein wichtiger Beitrag zur Kreislaufwirtschaft und zur Schonung natürlicher Rohmaterialien. Aktuell haben wir einen Anteil dieser dekarbonisierten Stoffe im Rohmaterial-Mix von etwa 10 %. Perspektivisch wollen wir diese Rate erhöhen.
Welche weiteren Hebel kommen zum Einsatz?
Stefan Schmorleiz: Der dritte und größte Hebel ist die Reduzierung des Anteils des Klinkers im Fertigprodukt Zement. Das kann zum Beispiel gelingen durch das teilweise Ersetzen des Klinkers durch andere reaktive Zumahlstoffe, die ähnliche festigkeitsbringende Eigenschaften haben wie der Klinker. Das kann der sogenannte Hüttensand sein, ein Beiprodukt der Roheisenproduktion, oder auch fein aufgemahlener, ungebrannter Kalkstein.
Wie wird Zement in Rüdersdorf hergestellt?
Welche Erfolge können Sie bereits verzeichnen?
Stefan Schmorleiz: Vor rund 30 Jahren hatten wir in Rüdersdorf einen Anteil des Klinkers in unseren Zementen von über 90 %. Heute sind wir bei nur noch rund 65 %. Wir arbeiten an mehreren Projekten und Spezialprodukten, um den Klinkerfaktor perspektivisch auf etwa 50 % zu reduzieren – ohne die Eigenschaften unserer Zemente und der späteren Betone zu beinträchtigen.
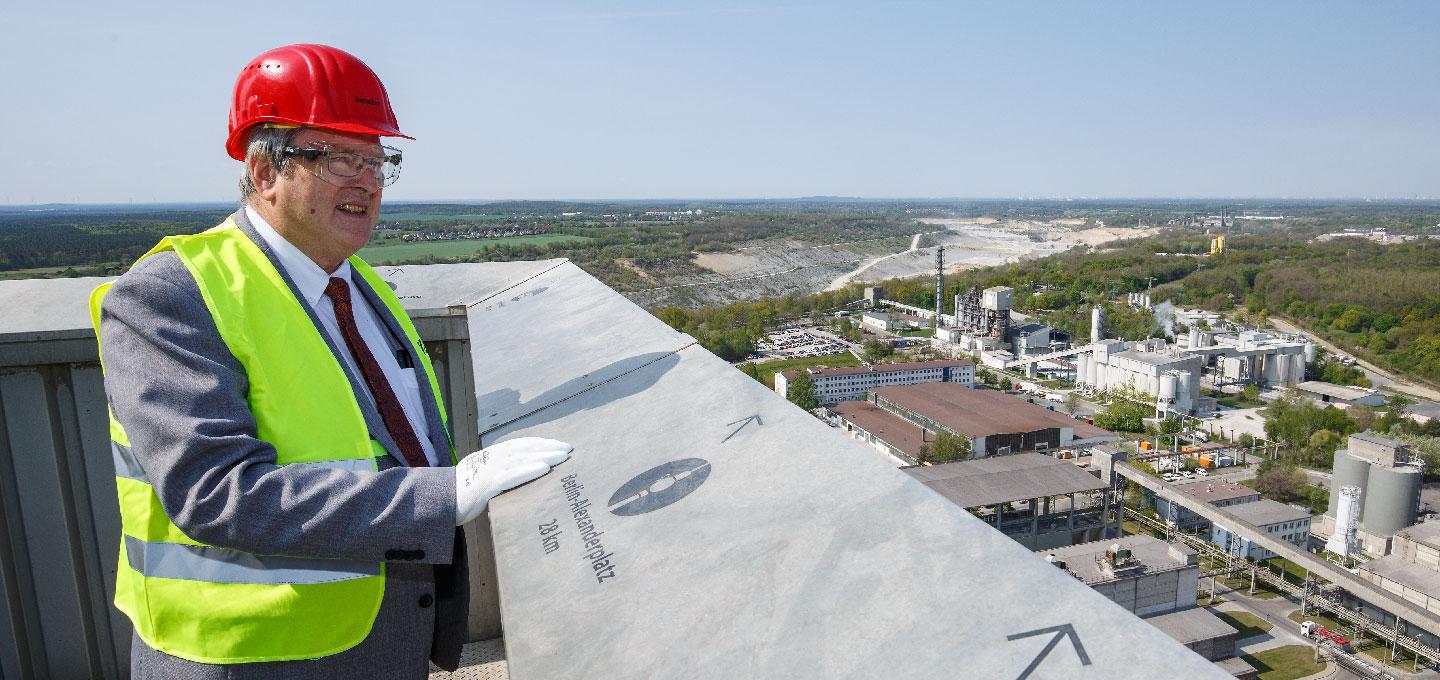
„Cemex ist ein Vorbild in Sachen Dekarbonisierung.“
Brandenburgs Minister für Wirtschaft, Arbeit und Energie, Prof. Dr.-Ing. Jörg Steinbach (SPD), war im Cemex-Werk in Rüdersdorf zu Gast und machte sich ein Bild von den Maßnahmen bezüglich der CO2-Neutralität.
Wie sieht es mit der Energie-Effizienz im Werk aus?
Stefan Schmorleiz: Im Vergleich zu anderen Werken erreicht das Rüdersdorfer Zementwerk bereits sehr hohe Energie-Effizienzgrade, sowohl in elektrischer als auch in thermischer Hinsicht. Gleichwohl befinden sich weitere Projekte in der Umsetzung, um die Energieverbräuche weiter zu reduzieren. Zum Beispiel wollen wir die Abwärme des Kühlers sowohl für Trocknungsvorgänge als auch zur Erzeugung von Wärme und Strom nutzen.
Im Vergleich zu anderen Werken erreicht das Rüdersdorfer Zementwerk bereits sehr hohe Energie-Effizienzgrade, sowohl in elektrischer als auch in thermischer Hinsicht.
Was haben diese Maßnahmen bisher gebracht?
Stefan Schmorleiz: Das kann man am besten mithilfe der Entwicklung unserer Netto-CO2-Emissionen, gemessen in kg CO2 je Tonne Zement, beantworten, einem international gängigen CO2-Kennwert für die Zementindustrie. In dem sogenannten CO2-Basisjahr 1990 lagen wir noch bei weit über 1000 kg CO2 je Tonne Zement. In den 30 Jahren von 1990 bis zum Jahr 2020 wurde dieser Wert bereits halbiert, zum Beispiel durch die Inbetriebnahme des sehr effizienten Ofens 5 im Jahr 1995 und dem Einsatz von Sekundärbrennstoffen seit den 2000er-Jahren. Auch hat man in dieser Zeit mit der Reduzierung des Klinkerfaktors im Zement begonnen. Wir haben die Geschwindigkeit der Reduzierungsmaßnahmen in den letzten drei Jahren weiter gesteigert; aktuell liegen wir nur noch bei knapp 400 kg. Das ist ein Top-Wert innerhalb des Konzerns und der gesamten deutschen Zementindustrie.
Was sind Ihre Ziele für die Zukunft?
Stefan Schmorleiz: Mit den genannten Maßnahmen kommen wir bald auf gut unter 300 kg CO2 je Tonne Zement. Das restliche CO2 sind dann unvermeidbare CO2-Emissionen, und diese müssen zum Erreichen der angestrebten CO2-Neutralität aus dem Abgasstrom abgeschieden und dann gespeichert oder anderweitig genutzt werden.
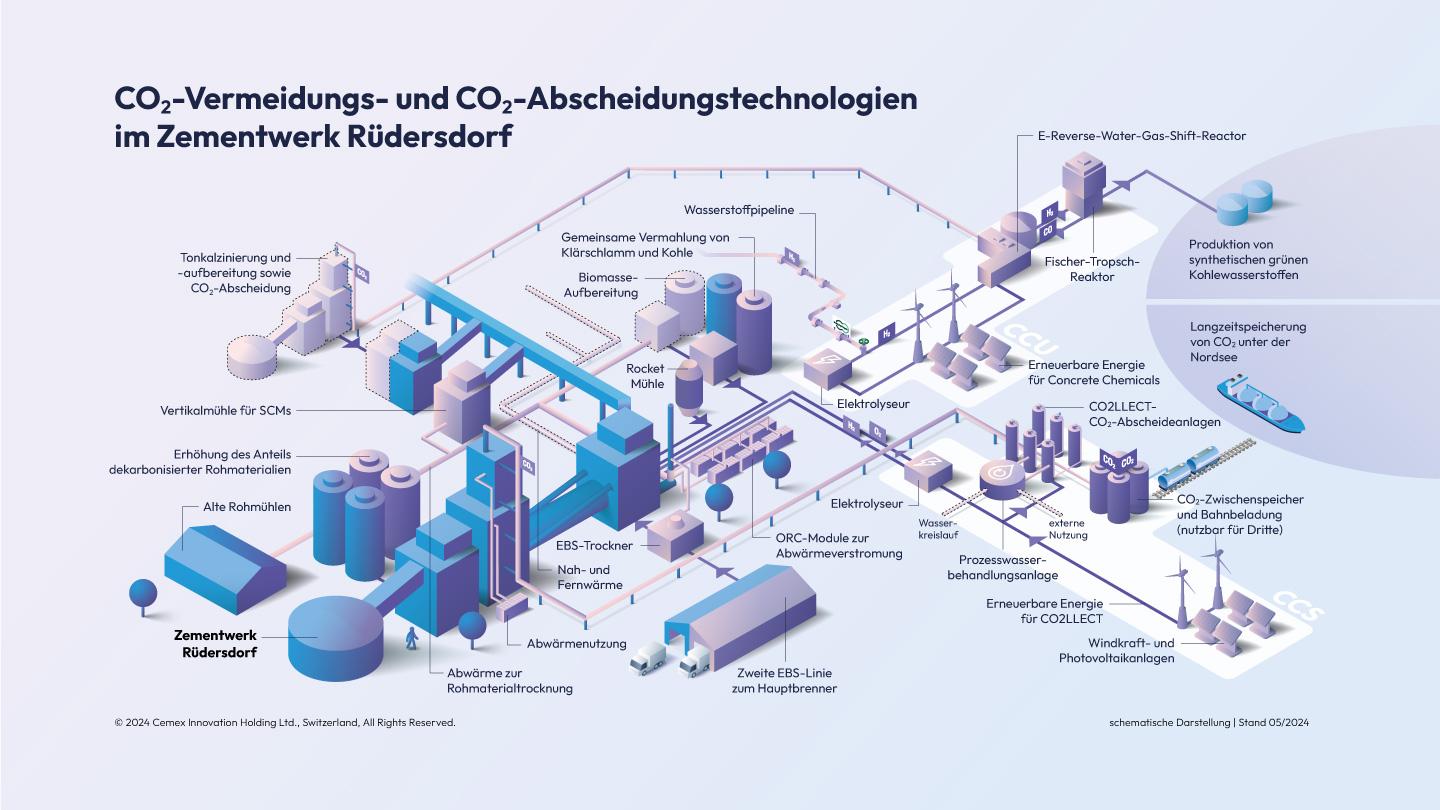
Das könnte Sie auch interessieren:
Unser bauwerk-Newsletter
Abonnieren Sie unseren Newsletter und erfahren Sie mehr über unsere Produkte, Strategie und Innovationen.
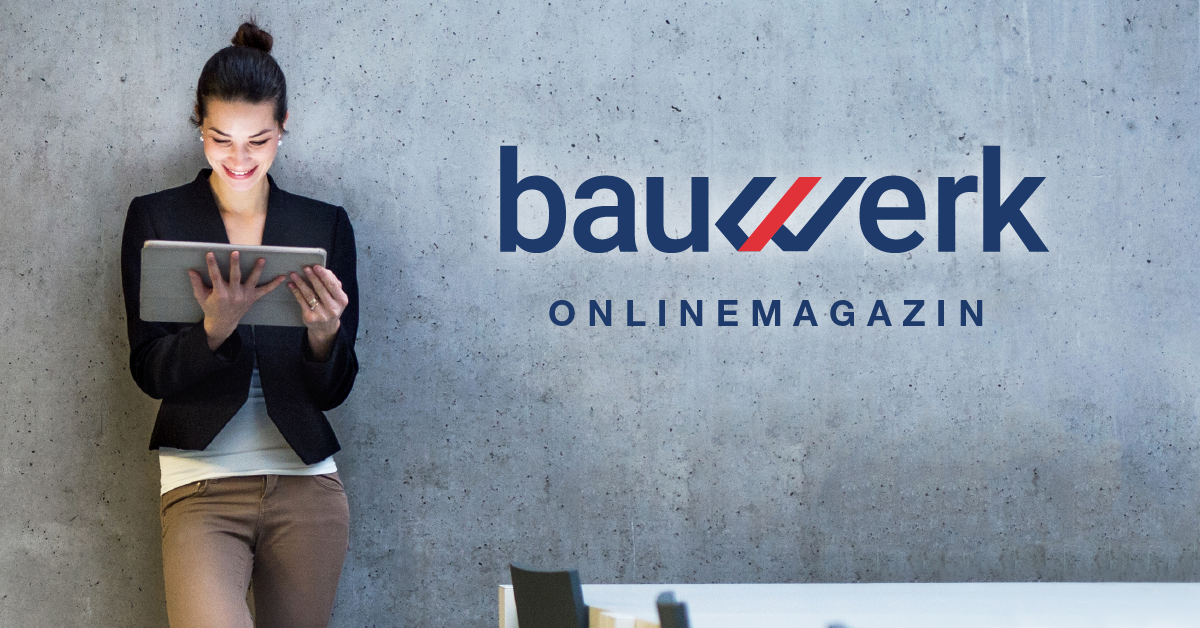